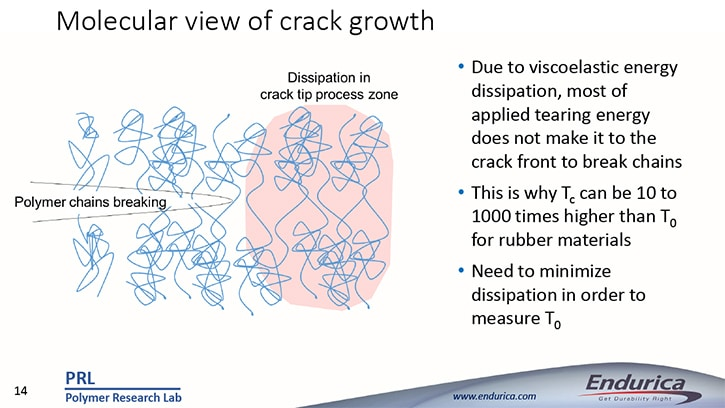
Getting a Quick Read on Durability with the Intrinsic Strength Analyser
A one-hour test on a benchtop instrument for the rubber lab screens materials for long-term fatigue performance.
See the world-leading rubber material testing equipment, the Intrinsic Strength Analyzer (ISA), in action. Based on classical elastomer characterization methodology, the ISA is used for materials development and monitoring mixing quality in the plant. Materials expert, Dr. Christopher Robertson, shows how it works and how it helps you Win on Durability.
- Fast and Reliable Testing: See how the ISA can quickly assess fatigue performance, providing actionable insights in just one hour.
- Improve Material Development: Learn how the ISA helps optimize rubber formulations for better long-term durability.
- Ensure Consistent Quality: Discover how this benchtop instrument is used to monitor mixing quality in real time, ensuring high standards in the plant.
- Expert Insights: Gain valuable knowledge from Dr. Christopher Robertson on leveraging cutting-edge testing methods to enhance material performance.
- Win on Durability: Understand how the ISA can help you stay ahead of the competition by focusing on fatigue resistance in rubber products.