Engineering elastomer components for critical railways
Elastomer components play a vital role in ensuring the longevity and performance of railway and rolling stock. Endurica’s advanced fatigue analysis software helps engineers design elastomer bearings, seals, and vibration isolation systems that withstand heavy loads, environmental stress, and long-term use. Our solutions ensure railway transport components and the wagons, carriages, and trucks that run on them are built to last, enhancing safety and reducing maintenance costs.
Maximize durability for railway elastomer components
Endurica’s fatigue analysis tools help railway component and railcar carriage manufacturers design elastomer components that perform reliably under the demanding conditions of this critical supply chain link. From extending part lifespan to minimizing maintenance, our solutions ensure your equipment stays in operation longer.
Load-Bearing Capacity
Optimize elastomeric bearings to accommodate the wear and tear of railway infrastructure, ensuring structural stability and longevity.
Weather Resistance
Simulate the effects of temperature changes, UV exposure, and moisture to ensure elastomer components remain durable under harsh environmental conditions.
Vibration Isolation
Design elastomer components that effectively absorb and isolate vibrations in rail systems, reducing wear and extending the operational life of critical parts.
Sealing and Flexibility
Ensure the durability of seals and expansion joints in infrastructure, accommodating movement while maintaining integrity over time.
Reduced Maintenance Costs
Accurately predict wear and fatigue, enabling the design of components that require less frequent maintenance for minimal operational disruptions.
Sustainable Solution Evaluation
Optimize component design for durability targets, including evaluating your latest compounds for environmentally-responsible and sustainable solutions early in the design process.
Industry Requirement | Endurica Solution | Result/Benefit |
---|---|---|
Support Heavy Loads in Bridges | Endurica CL™ for fatigue life prediction. | Ensure elastomer bearings in bridges can withstand heavy loads, enhancing structural stability and longevity. |
Absorb Vibration in Rail Systems | Endurica EIE™ for vibration fatigue analysis | Improve vibration isolation in rail systems, reducing wear and extending the lifespan of critical components. |
Resilience to Environmental Factors | Endurica EIE™ for temperature-dependent fatigue analysis. | Design elastomer parts that resist UV, moisture, and temperature fluctuations, increasing durability in outdoor infrastructure. |
Crack Growth and Wear in Bridge Bearings | Endurica DT™ for crack growth and wear simulation. | Predict crack propagation and wear in bearings, helping to plan for maintenance and improve the lifespan of critical components. |
Minimize Maintenance Downtime | fe-safe/Rubber™ for predictive maintenance scheduling. | Accurately predict when components need maintenance, reducing downtime and operational costs. |
Strengthen the durability of your rail components
Partner with Endurica to design elastomer components that meet the toughest railway challenges. Our advanced fatigue analysis solutions ensure your components withstand heavy loads, vibrations, and extreme environmental conditions.
Contact UsCase Study
Delkor rail enhances rail system durability with Endurica’s fatigue analysis
Delkor Rail utilized Endurica’s fatigue analysis tools to improve the durability of their vibration isolation systems used in rail tracks. By predicting fatigue life under multi-channel loads, Delkor Rail optimized material selection and extended the lifespan of critical components, ensuring long-term performance and reliability in demanding rail environments.
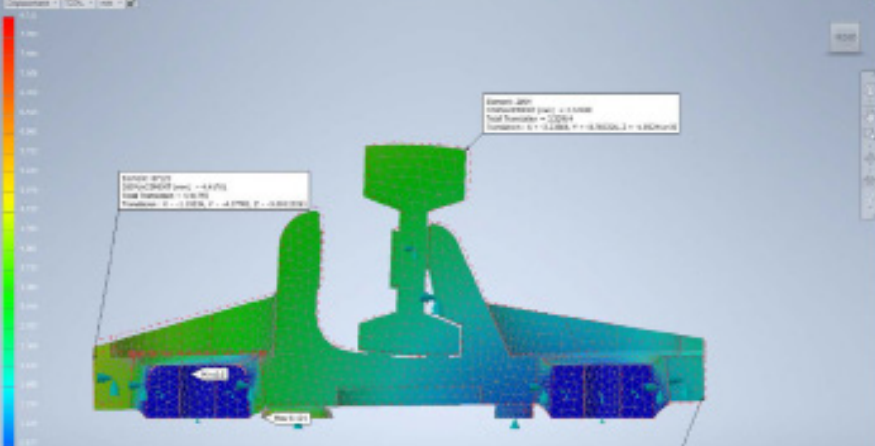