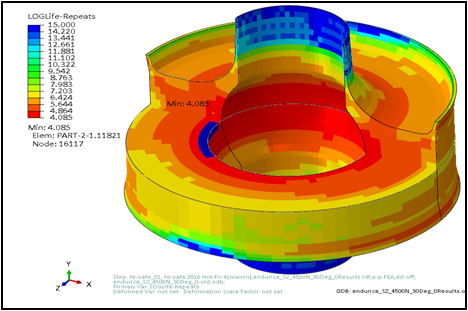
The Challenge
Suspension components are subject to significant wear due to constant stress from varied road conditions. Tenneco needed a way to predict fatigue and optimize product designs early to avoid costly failures, minimize downtime, and meet high-performance standards.
The Solution
Since 2010, Tenneco has utilized Endurica’s fatigue analysis tools to streamline the development of high-performance suspension components.
With Endurica CL™, Tenneco simulated fatigue life to detect potential failure points early in the design process. This predictive capability allowed them to optimize product geometry and reduce reliance on costly physical testing.
Using Endurica EIE™, Tenneco simulated real-world multi-channel loading scenarios, ensuring that components could withstand demanding road conditions without compromising performance. This provided critical insights into material selection and component durability, minimizing the risk of premature failures.
Additionally, Endurica DT™ enabled Tenneco to model crack growth behavior and extend component lifespan. By incorporating these predictive tools, Tenneco reduced testing cycles, improved product quality, and ensured their suspension systems met the highest reliability standards, helping them stay ahead in the competitive mobility solutions market.
Tenneco has worked with Endurica since 2010
−Josh Goossens attended Endurica’s 2nd material training class in Spring 2010
−Tenneco started with performing hyperelastic testing internally in 2011 on 1 EM frame
- In 2014 Tenneco decided to build an internal material test lab to perform all testing required for Endurica simulations and began development of the FCG software
- 2015 a fatigue testing laboratory was repurposed into an Endurica material test lab.
- 2015 started internal FCG testing on 1 machine and began using the Endurica software
- 2017 Expanded the internal test lab capacity with the purchase of 2 additional E/M frames, 3 high speed hydraulic machines, a CoesfeldISA
- 2017 Sponsored the Endurica development of the stress softening feature in Endurica DT
- 2017 Presented at the Society of Automotive Engineers NVC conference and at ECCMR – European Conference on Constitutive Models for Rubbers
- 2021 To date, Tenneco had fully tested ~50 compounds and performed 2100 Endurica fatigue simulations
Results:
- Increased Product Lifespan: Fatigue simulations helped extend the life of suspension components, reducing failures and improving reliability.
- Reduced Physical Testing Costs: Predictive tools minimized the need for costly prototypes and shortened development cycles.
- Optimized Material Selection: Multi-channel load analysis ensured that components met durability standards across diverse operating conditions.
- Enhanced Market Competitiveness: Faster iterations and high-quality outputs allowed Tenneco to deliver advanced solutions that met industry demands efficiently.
Endurica’s methods give us robust life-prediction capabilities and are really good tools to help us determine which design option is the best. We’re using it up-front, during development, and during production — we’re using it everywhere we can.
Guy Smith Chief Engineer/CAE Manager,
Tenneco Clevite Elastomers

Feature | Solution | Result |
---|---|---|
Fatigue Life Prediction | Endurica CL for fatigue life prediction | Identified early failure risks, extending component lifespan. |
Crack Growth Prevention | Endurica DT for crack growth analysis. | Minimized early failures, reducing maintenance costs and downtime. |
Multi-Channel Load Analysis | Endurica EIE for complex real-world load and stress simulations and analysis. | Ensured consistent performance under diverse operational conditions. |
Trusted by World-Class Innovators: Join Leading Companies Optimizing Their Durability with Endurica Durability Solutions
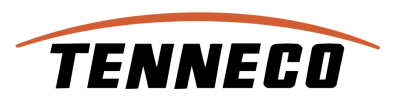
Tenneco
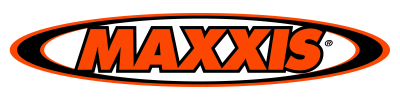
Maxxis
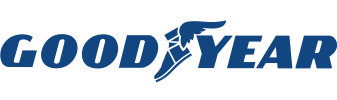
Goodyear
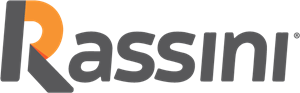