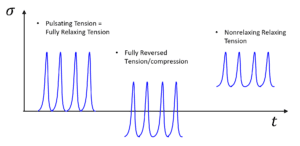
Figure 1. Constant amplitude cycles at three different mean strains.
Rubber and metal are very different materials that exhibit very different behaviors. Consider the effect of mean strain or stress on the fatigue performance of these materials. Figure 1 illustrates a few typical constant amplitude strain cycles, each at a different level of mean strain. If the stress amplitude is equal to the mean stress, we say that we have pulsating tension or fully relaxing tension. If the mean stress is zero, we say that we have fully reversed tension/compression. If the minimum stress is always positive, then we have nonrelaxing tension (i.e. always under load). Nonrelaxing cycles are quite common in applications. Examples include: pre-loads applied during installation; swaging of a bushing to induce compressive pre-stresses, interference fits, self-stresses occurring due to thermal expansion/contraction; and in tires, shape-memory effects of textile cords.
In metal fatigue analysis, it is customary to define the effect in terms of stress amplitude σa and mean stress σm, relative to the yield stress σy and the ultimate stress σu, as shown in Figure 2. Below the fatigue threshold stress σ0, indefinite life is predicted. The Haigh (or Goodman)
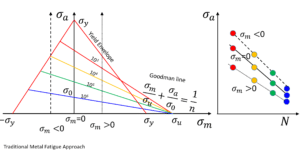
Figure 2. Haigh diagram (left) and Wohler curves (right) showing mean strain effects on fatigue life for a metal.
diagram (left) maps fatigue life as a function of these parameters [1]. Wohler curves (right) provide similar information. For metals, a simple rule may be applied universally: increasing mean strain is detrimental fatigue life. It is also commonly assumed for metals that the critical plane is perpendicular to maximum principal stress direction.
There are many ways that rubber materials differ from metallic materials. At the atomic scale, rubber is composed of long chain molecules experiencing constant thermal motion while interlinked with a permanent network topology. This structure permits large, elastic/reversible straining to occur. Metals could not be more different, existing as individual atoms packed into well-ordered crystals with occasional dislocations or lattice vacancies. This structure permits only vanishingly small strains before inelastic deformation occurs. At the meso scale, rubber is typically a composite material containing fillers such as carbon black, silica or clay, as well as other chemical agents. The mesoscale of a metal is generally described in terms of crystalline grain boundaries and inclusions or voids. Rubber exhibits many “special effects” that are not seen in metals: rate and temperature dependence, ageing, cyclic softening. It is unsurprising that analysis methods for rubber differ substantially from those applied for metals.
Rubber’s fatigue performance has a more complex dependence on mean strain. For amorphous (ie non-crystallizing) rubbers, increasing mean strain reduces the fatigue life, as with metals. But for rubbers that exhibit strain-induced crystallization, mean strain can greatly increase fatigue life, as illustrated in Figure 3. Fatigue simulations therefore must take account of the strain crystallization effect.
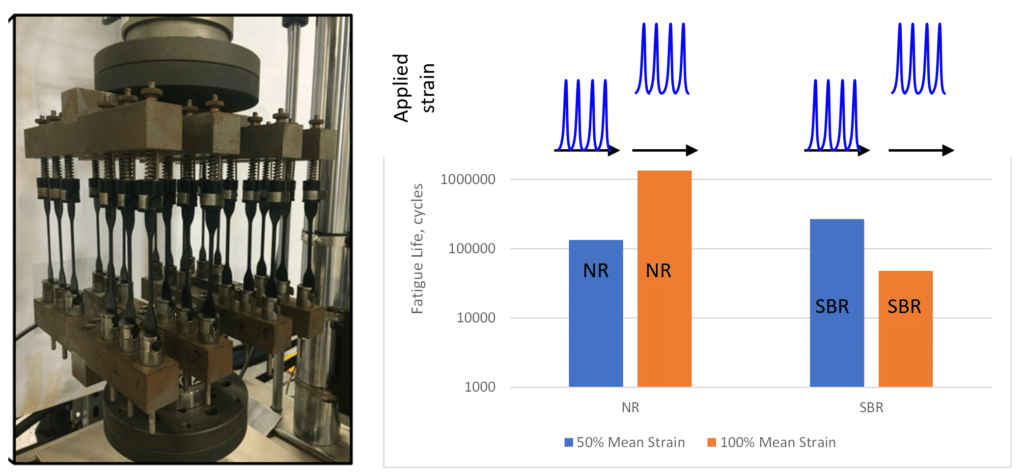
Figure 3. Fatigue tests run in simple tension under constant amplitude show a significant increase in life for Natural Rubber (NR), which strain crystallizes, and a decrease of life for Styrene Butadiene Rubber (SBR) which is amorphous [2].
Table 1. Models for computing crack growth rate in amorphous and strain-crystallizing rubbers.
Rubber’s fatigue behavior may be plotted in a Haigh diagram, but the contours can be quite different than for metals. In metal fatigue analysis, it is assumed that cracks always develop perpendicular to the max principal stress direction. This is not always true for rubber, especially in cases involving strain crystallization and nonrelaxing loads. For rubber fatigue analysis it is therefore required to use critical plane analysis [5], in which fatigue life is computed for many potential crack orientations, and in which the crack plane with the shortest life is identified as the most critical plane. Figure 4 shows the dependence of the fatigue life and the critical plane orientation on strain amplitude and mean strain. A sphere is plotted for each pair of strain amplitude and mean strain coordinates, on which the colors represent fatigue life, and unit normal vectors indicate critical plane orientations. It can be seen that different combinations of mean strain and strain amplitude can produce a range of crack plane orientations.
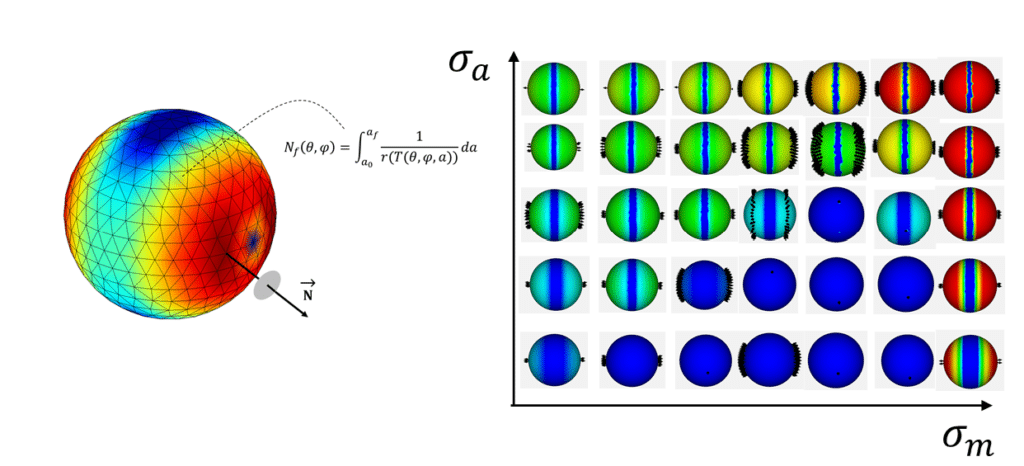
Figure 4. Critical plane analysis consists in integrating the crack growth rate law for every possible crack orientation, and identifying the orientation that produces the shortest life (left). Each point in the Haigh diagram (right) is associated with its own critical plane orientation.
The Haigh diagrams for natural rubber (NR) and for styrene butadiene rubber (SBR) are shown in Figure 5. In these images, red represents short fatigue life, and blue long life. For natural rubber (on the left), the long-life region of the Haigh diagram exhibits a notable dome-like shape, indicative of a beneficial effect of mean strain under the influence of strain-induced crystallization. In contrast, SBR always exhibits decreased fatigue life as mean strain increases. Even so, the Haigh diagram for SBR has a nonlinear character associated with the material’s hyperelasticity that is also distinct from a metal.
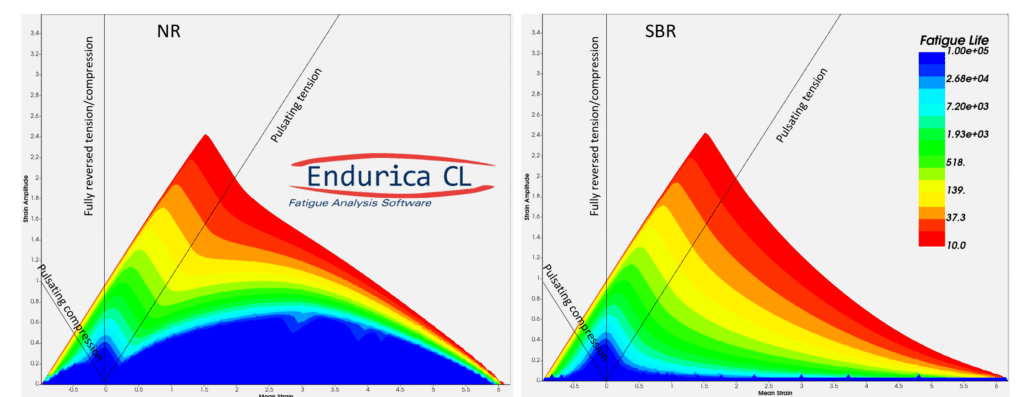
Figure 5. Haigh diagrams computed for NR (left) and for SBR (right) rubbers.
It should be noted that the strain crystallization effect in rubber depends on temperature. At colder temperatures, the effect is stronger, and at higher temperatures it is weaker. Figure 6 compares experimental Haigh diagrams [6] (top) for a crystallizing rubber to computed results (bottom) for three temperatures.
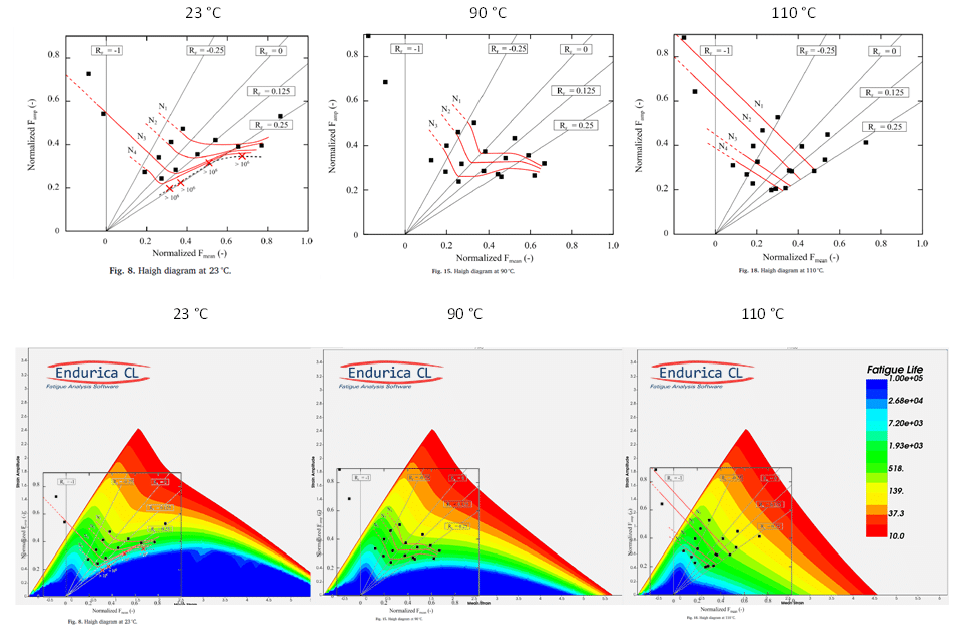
Figure 6. Experimental Haigh diagram [6] for natural rubber at 3 temperatures (top), compared to computed Haigh diagram (bottom). Increasing temperature tends to reduce the beneficial effect of strain crystallization.
References
[1] Stephens, R. I., Fatemi, A., Stephens, R. R., & Fuchs, H. O. (2000). Metal fatigue in engineering. John Wiley & Sons.
[2] Ramachandran, Anantharaman, Ross P. Wietharn, Sunil I. Mathew, W. V. Mars, and M. A. Bauman. (2017) “Critical plane selection under nonrelaxing simple tension with strain crystallization.” In Fall 192nd technical meeting of the ACS Rubber Division, pp. 10-12.
[3] Mars, W. V. (2009). Computed dependence of rubber’s fatigue behavior on strain crystallization. Rubber Chemistry and Technology, 82(1), 51-61.
[4] Harbour, Ryan J., Ali Fatemi, and Will V. Mars. “Fatigue crack growth of filled rubber under constant and variable amplitude loading conditions.” Fatigue & Fracture of Engineering Materials & Structures 30, no. 7 (2007): 640-652.
[5] Mars, W. V. (2021). Critical Plane Analysis of Rubber. Fatigue Crack Growth in Rubber Materials: Experiments and Modelling, 85-107.
[6] Ruellan, Benoît, J-B. Le Cam, I. Jeanneau, F. Canévet, F. Mortier, and Eric Robin. “Fatigue of natural rubber under different temperatures.” International Journal of Fatigue 124 (2019): 544-557.